Metallized Plastic Film Capacitors
Metallized plastic film capacitors come in a variety of forms, using different materials. They are useful in many applications, especially as leaded components.
Home » Electronic components » this page
Capacitor Tutorial Includes:
Capacitor uses
Capacitor types
Electrolytic capacitor
Ceramic capacitor
Ceramic vs electrolytic
Tantalum capacitor
Film capacitors
Silver mica capacitor
Super capacitor
Surface mount capacitors
Specifications & parameters
How to buy capacitors - hints & tips
Capacitor codes & markings
Conversion table
Plastic film capacitors come in several forms. Essentially they use a metallized plastic film to enable the electrodes to the created and spaced apart from one another.
The different types of metallized plastic film capacitor provide different properties, each suited to slightly different applications.
The values of metallized plastic film capacitors may range anywhere from several picofarads to a few microfarads dependent upon the actual type. Normally they are non-polar. In general they are good general-purpose capacitors that may be used for a variety of purposes, although their high frequency performance is not usually as good as that of the ceramic types.
Film capacitor basics
Film capacitors are known under a variety of different names including, plastic film capacitors, film dielectric capacitors, or polymer film capacitors, and metallised film capacitors.
The basic concept of this type of capacitor is the insulating plastic film as the dielectric. This may sometimes be combined with paper as carrier of the electrodes.
The dielectric films are drawn to an extremely thin film - hence the name. This is then used as the dielectric material between the two electrodes or plates.
The dielectric and the electrode films or plates are wound together into a cylinder, or several layers are placed together and the external connections added.
A variety of different plastic films may be used. Each type has its own properties as detailed in the section below on dielectrics.
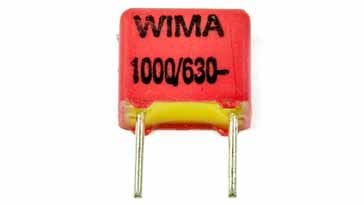
Film capacitor construction
There are two main formats for the construction of film capacitors. The actual construction type depends upon the dielectric material used and the requirements for the physical construction.
- Film foil: This form of film capacitor has two metal foil electrodes that are separated by the plastic film. The terminals are typically connected to the end-faces of the electrodes by means of welding or soldering.
- Metallised film: In this type of film capacitor the plastic film has a very thin layer of metallisation deposited onto the film. The thin metal layer is typically only 0.02 to 0.1µm thick. This is vacuum deposited onto the plastic film. My leaving a small area free of metallisation at either end, it is possible to connect the metallisation to one connection or the other of the film capacitor.
Some special types of construction may be used for film capacitors that are required for niche or specialist applications. These are not widely seen.
Self healing
One aspect of film capacitors is that of self-healing. The self healing or clearing occurs when defects caused by small pinholes, flaws in the film, or external voltage transients. Any arcing vapourises the thin metallisation of the film around the failure thereby removing the metallisation in the area of the flaw and removing any conductive material in the area. If there is no conductive material, the capacitor cannot short across between the plates and failure is removed.
Film capacitor dielectrics
Many of the dielectric are known by their common names and they also have abbreviations.
As there is a wide variety of different dielectrics for the different types of film capacitor, a summary of the different types is given below.
- Polyester / Mylar PET: This type of plastic film capacitor is manufactured in both metallised wound versions and the film foil types. These film capacitors are low cost types and relatively small for their capacitance. They are generally used for general purpose electronic applications.. Their maximum temperature rating of 125°C enables them to be manufactured as surface mount components although in this format they are not nearly as widely used as ceramic types that have almost cornered them market for values below 1µF.
Polyester film capacitor - Polycarbonate, PC: Although a very successful and useful form of film capacitor, this type is no longer made because the manufacturer of the film ceased production of it around the year 2000. The nearest replacement type is generally considered to be the PP, polypropylene dielectric.
This type of film capacitor was manufactured as wound types as well as film / foil. The capacitors have a low dissipation factor and they are relatively temperature stable, often as low as ±80ppm over the entire temperature range. As a result they are often used in timing circuits, filters and other precision analogue applications.
This type of film capacitor introduces moderate level of loss which can increase with frequency. It has a very high insulation resistance. . . . . . Read more about polycarbonate capacitors - Polystyrene: These film capacitors are also sold under the trade name Styroflex. They used to be known as being cheap general purpose capacitors with high stability and low dissipation and leakage.
The films could not be made any thinner than 10µm and this limited the capacitance levels that could be achieved. The temperature ratings were also low with a maximum of 85°C operating temperature. As a result they are no longer widely used, normally being replaced by polyester types.
Polystyrene film capacitor - Polythene Sulphide, PPS: These film capacitors are only manufactured as the metallised film types. They offer a very low temperature variation over the temperature range, typically ± 1.5%. The dissipation factor is quite small as the frequency dependence.
These film capacitors are well suited to applications where frequency stability is paramount and in applications where high temperatures may be encountered. They may also be found in surface mount formats, although costs tend to be much higher than the ceramic counterparts. - Polyethylene naphthalate, PEN: These film capacitors are only produced as metallised film types. They belong to the polyester family but provide a better high temperature resilience and performance. As a result they are more suited to SMD applications where the soldering process takes temperatures much higher than they do for leaded versions.
The temperature and frequency dependence figures for PEN capacitors are very similar to those of the PET polyester versions. However as a result of the smaller relative permittivity, the physical capacitor size is larger for a given capacitance.
A special high voltage PEN dielectric is available and this is ideal for many high voltage and high temperature applications.
Overall PEN film capacitors are used for non-critical filtering coupling and decoupling in electronic circuits where temperature dependencies are not important. - Polytetrafluoroethylene, PTFE: PTFE film capacitors are manufactured in both metallised film and film / foil variants. One of the key features of this form of film capacitor is its very high temperature resistance - it can withstand temperatures of 200°C and above. There are difficulties in manufacturing the PTFE film to a sufficiently tight tolerance. As a result these capacitors tend to be expensive, and they are manufactured by a limited number of manufacturers. In view of this the capacitors tend to be reserved for specialist applications.
- Polypropylene, PP: . . . . . Read more about polypropylene capacitors
These are the main types of film capacitor that will be seen in most applications. There are other types, but these are comparatively rarely seen.
Metal film capacitor summary
The table below provides some of the salient features about some of the more widely used metallised plastic film capacitors that can be taken into consideration when designing circuits or replacing old components.
Metal Film Capacitor Summary | ||||
---|---|---|---|---|
Parameter | PET | PEN | PPS | PP |
Relative permittivity @ 1 kHz | 3.3 | 3.0 | 3.0 | 2.2 |
Minimum film thickness (µm) | 0.75 | 0.1 | 1.2 | 2 |
Moisture absorption (%) | Low | 0.4 | 0.05 | <0.1 |
Dielectric strength (V/µm) | 580 | ~500 | 470 | 650 |
Capacitor DC voltage range (V) | 50 - 100 | 10 - 250 | 10 - 100 | 40 - 2000 |
Capacitance range | 100pf – 22µF | 100pF – 1µF | 100pF – 0.47µF | 100pF – 10 µF |
Dissipation factor a 1 kHz | 50 - 200 | 40 - 80 | 2 - 15 | 0.5 - 5 |
Dissipation factor a 10 kHz | 100 - 150 | 50 - 150 | 2.5 - 25 | 2 - 10 |
Dissipation factor a 100 kHz | 170 - 300 | 120 - 300 | 10 -6- | 2 -25 |
Dissipation factor a 1 MHz | 200 - 350 | 20 -70 | 5 - 40 |
There are many different types of metallized film and plastic film capacitors that are available. Even though they use a simialr form of technology, the variation of dielectrics means that they have a variety of performance parameters and careful selection of the type of dielectric is neceessary to provide the optimum performance.
Written by Ian Poole .
Experienced electronics engineer and author.
More Electronic Components:
Batteries
Capacitors
Connectors
Diodes
FET
Inductors
Memory types
Phototransistor
Quartz crystals
Relays
Resistors
RF connectors
Switches
Surface mount technology
Thyristor
Transformers
Transistor
Unijunction
Valves / Tubes
Return to Components menu . . .